Melt vs Strength Models: Unlocking Material Performance Secrets
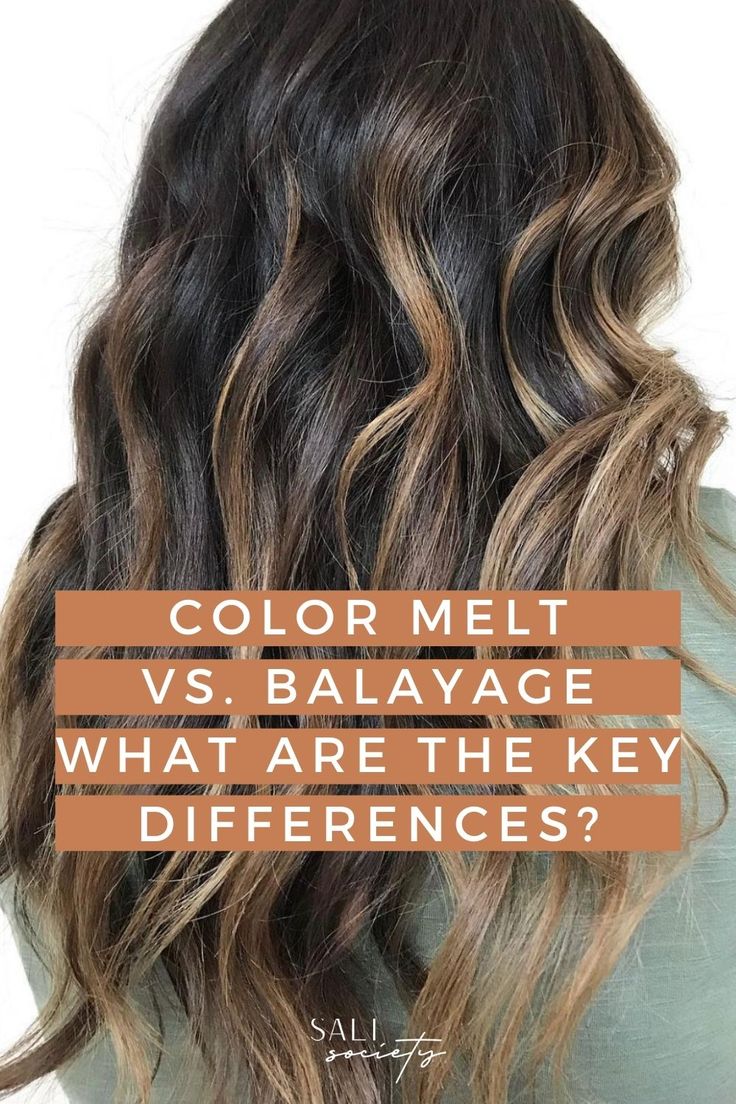
Understanding the behavior of materials under different conditions is crucial for industries ranging from manufacturing to aerospace. Two key models, Melt Models and Strength Models, play a pivotal role in predicting material performance. These models help engineers and scientists optimize material usage, enhance product durability, and ensure safety. Whether you’re an industry professional or a curious learner, this post will guide you through the essentials of these models, their applications, and how they unlock material performance secrets. (Material Science, Engineering Models, Material Performance)
What Are Melt Models?

Melt models focus on understanding how materials behave when subjected to high temperatures, leading to melting or softening. These models are essential in processes like casting, molding, and 3D printing, where materials transition from solid to liquid states. By predicting melting points and behaviors, engineers can optimize production processes and select the right materials for specific applications. (Melting Point, Material Behavior, Manufacturing Processes)
Key Applications of Melt Models
- Metal Casting: Ensures precise control over melting and solidification.
- Polymer Processing: Helps in extrusion and injection molding.
- Additive Manufacturing: Optimizes material flow in 3D printing.
💡 Note: Melt models require accurate data on thermal properties for reliable predictions.
What Are Strength Models?

Strength models analyze a material’s ability to withstand external forces without deformation or failure. These models are critical in designing structures, vehicles, and machinery that require high durability and safety. By simulating stress, strain, and fatigue, engineers can predict material performance under various conditions. (Material Strength, Stress Analysis, Durability Testing)
Key Applications of Strength Models
- Structural Engineering: Ensures buildings and bridges can bear loads.
- Automotive Industry: Enhances vehicle safety and performance.
- Aerospace: Predicts material behavior under extreme conditions.
⚙️ Note: Strength models rely on mechanical properties like tensile strength and elasticity.
Comparing Melt vs Strength Models
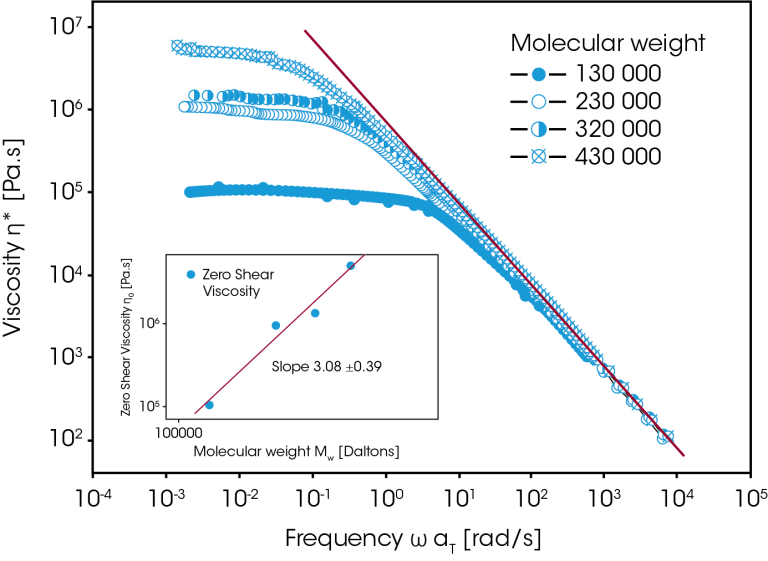
While both models are fundamental in material science, they serve distinct purposes. Melt models focus on thermal behavior, whereas strength models emphasize mechanical performance. Below is a comparison table highlighting their differences:
Aspect | Melt Models | Strength Models |
---|---|---|
Focus | Thermal Behavior | Mechanical Performance |
Key Parameters | Melting Point, Thermal Conductivity | Tensile Strength, Elasticity |
Primary Applications | Casting, 3D Printing | Structural Design, Automotive |
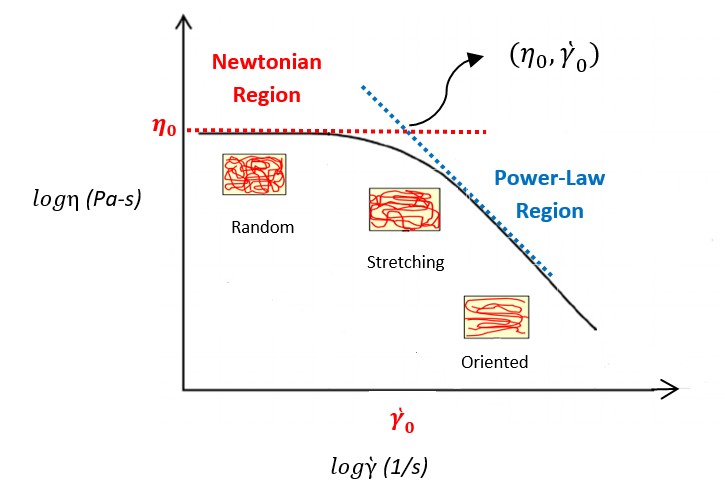
How to Choose the Right Model for Your Needs

Selecting between melt and strength models depends on your specific application. Here’s a quick checklist to guide your decision:
- Identify the Primary Concern: Is it thermal behavior or mechanical strength?
- Evaluate Material Properties: Consider melting points, tensile strength, and elasticity.
- Assess Application Requirements: Determine if the focus is on manufacturing processes or structural integrity.
Unlocking Material Performance Secrets

By leveraging melt and strength models, industries can unlock material performance secrets, leading to innovation and efficiency. These models enable precise predictions, reduce trial-and-error costs, and ensure product reliability. Whether you’re developing cutting-edge materials or optimizing existing processes, understanding these models is key to success. (Material Innovation, Process Optimization, Product Reliability)
What is the main difference between melt and strength models?
+Melt models focus on thermal behavior, such as melting points, while strength models analyze mechanical performance, like tensile strength.
Which industries benefit most from melt models?
+Industries like metal casting, polymer processing, and additive manufacturing benefit significantly from melt models.
How do strength models enhance product safety?
+Strength models predict material behavior under stress, ensuring products can withstand external forces without failure, thus enhancing safety.
In summary, melt and strength models are indispensable tools in material science and engineering. By understanding their applications and differences, professionals can make informed decisions, optimize processes, and drive innovation. Whether you’re melting metals or testing tensile strength, these models unlock the secrets to material performance, paving the way for advancements across industries. (Material Science, Engineering Innovation, Process Optimization)