6000 Series Aluminum in Aerospace: Key Applications Explained
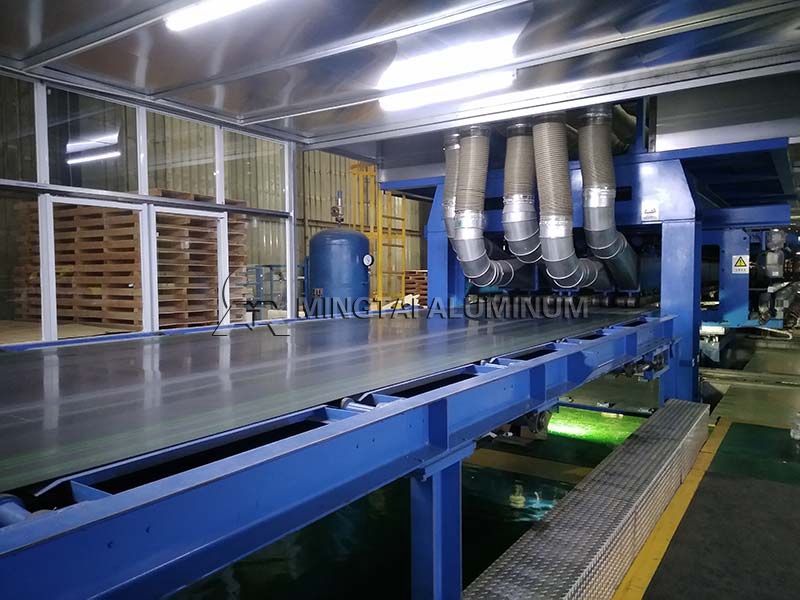
The aerospace industry demands materials that combine strength, lightweight properties, and corrosion resistance. Among these, the 6000 series aluminum stands out as a cornerstone material. Known for its versatility and reliability, this alloy series is widely used in aircraft manufacturing, from structural components to interior fittings. In this post, we’ll explore the key applications of 6000 series aluminum in aerospace, its unique properties, and why it remains a top choice for engineers and manufacturers alike. Whether you're an industry professional or an enthusiast, understanding this material’s role in aerospace can provide valuable insights into modern aviation technology.
What Makes 6000 Series Aluminum Ideal for Aerospace?

The 6000 series aluminum is primarily alloyed with magnesium and silicon, which enhances its strength and weldability. This combination makes it an excellent choice for aerospace applications where lightweight materials are critical for fuel efficiency and performance. Key properties include:
- High Strength-to-Weight Ratio: Essential for reducing aircraft weight without compromising durability.
- Corrosion Resistance: Vital for withstanding harsh environmental conditions at high altitudes.
- Formability: Allows for complex shapes and designs, crucial for aerospace components.
These characteristics make the 6000 series aluminum a preferred material for various aerospace applications, ensuring both safety and efficiency. (aerospace materials,aluminum alloys,lightweight aircraft components)
Key Applications of 6000 Series Aluminum in Aerospace

1. Aircraft Structural Components
The 6000 series aluminum is extensively used in the construction of aircraft wings, fuselages, and stringers. Its ability to withstand stress and fatigue makes it ideal for these critical parts. For instance, the 6061 alloy, a popular variant, is commonly used in wing structures due to its excellent machinability and weldability.
2. Interior Fittings and Cabin Components
Beyond structural applications, the 6000 series aluminum is also used in aircraft interiors, including seats, overhead bins, and galley structures. Its lightweight nature helps reduce overall aircraft weight, contributing to fuel efficiency. Additionally, its corrosion resistance ensures longevity even in humid cabin environments.
3. Aerospace Fasteners and Hardware
Fasteners like bolts, screws, and rivets made from 6000 series aluminum are essential for assembling aircraft components. These fasteners offer the necessary strength while minimizing weight, a critical factor in aerospace engineering. The 6063 alloy, known for its extrudability, is often used for manufacturing these parts.
Application | Common Alloy | Key Benefit |
---|---|---|
Aircraft Wings | 6061 | High Strength & Weldability |
Interior Fittings | 6063 | Lightweight & Corrosion Resistance |
Fasteners | 6061/6063 | Strength & Reduced Weight |

✈️ Note: While 6000 series aluminum is highly versatile, it’s essential to select the right alloy variant based on specific application requirements.
Why Choose 6000 Series Aluminum for Aerospace?

The 6000 series aluminum offers a unique blend of properties that make it indispensable in aerospace manufacturing. Its cost-effectiveness, coupled with its ability to meet stringent industry standards, ensures its continued use in both commercial and military aircraft. Moreover, advancements in alloying techniques have further enhanced its performance, making it a future-proof material for the aerospace sector.
- ✔️ High strength-to-weight ratio for improved fuel efficiency.
- ✔️ Excellent corrosion resistance for long-term durability.
- ✔️ Superior formability for complex aerospace designs.
- ✔️ Cost-effective compared to other high-performance materials.
In summary, the 6000 series aluminum plays a pivotal role in the aerospace industry, offering a perfect balance of strength, weight, and cost. Its applications range from critical structural components to interior fittings, making it a material of choice for modern aircraft. As aerospace technology continues to evolve, the 6000 series aluminum will undoubtedly remain at the forefront of innovation. (aerospace engineering,aluminum in aviation,aircraft manufacturing)
What is the most common alloy in the 6000 series used in aerospace?
+
The 6061 alloy is the most widely used in aerospace due to its high strength, weldability, and corrosion resistance.
Why is lightweight material important in aerospace?
+
Lightweight materials reduce aircraft weight, leading to improved fuel efficiency, lower operating costs, and enhanced performance.
Can 6000 series aluminum be used in high-temperature environments?
+
While it offers good corrosion resistance, the 6000 series is not ideal for high-temperature applications. Other alloys like the 2000 or 7000 series are better suited for such conditions.