3D Model for Servo Torque Testing: A Comprehensive Guide

<!DOCTYPE html>
Servo torque testing is a critical process in ensuring the performance and reliability of servo motors. With the advent of 3D modeling, engineers and technicians can now simulate and analyze servo torque more efficiently. This guide provides a step-by-step approach to creating and utilizing a 3D model for servo torque testing, ensuring accuracy and precision in your results. (servo torque testing, 3D modeling for servos, servo motor performance)
Why Use 3D Modeling for Servo Torque Testing?

3D modeling offers several advantages for servo torque testing, including:
- Visualization: Better understanding of servo motor mechanics and torque distribution.
- Simulation: Ability to simulate various load conditions and scenarios.
- Accuracy: Precise measurements and predictions of torque values.
- Cost-Effectiveness: Reduces the need for physical prototypes and extensive testing.
(3D modeling advantages, servo torque simulation, torque distribution analysis)
Steps to Create a 3D Model for Servo Torque Testing

Step 1: Define Project Requirements
Before starting, clearly define the objectives of your servo torque testing project. This includes:
- Servo motor specifications
- Load conditions
- Expected torque range
📌 Note: Accurate project requirements ensure a relevant and effective 3D model.
(project requirements, servo motor specifications, load conditions)
Step 2: Choose the Right Software
Select a 3D modeling software that supports servo motor simulations. Popular options include:
- SolidWorks
- ANSYS
- COMSOL Multiphysics
(3D modeling software, servo motor simulations, SolidWorks, ANSYS)
Step 3: Model the Servo Motor
Create a detailed 3D model of the servo motor, including:
- Rotor and stator components
- Bearings and housing
- Shaft and coupling mechanisms
📌 Note: Ensure the model accurately represents the physical servo motor for reliable results.
(servo motor modeling, rotor and stator, shaft and coupling)
Step 4: Apply Load Conditions
Simulate various load conditions to test servo torque. This can include:
- Static loads
- Dynamic loads
- Varying speeds and positions
(load conditions, static and dynamic loads, servo torque testing)
Step 5: Analyze and Validate Results
Review the simulation results to analyze torque values and motor performance. Validate the findings against real-world data or theoretical expectations.
📌 Note: Validation ensures the accuracy and reliability of your 3D model.
(simulation results, torque analysis, model validation)
Checklist for Successful 3D Servo Torque Testing
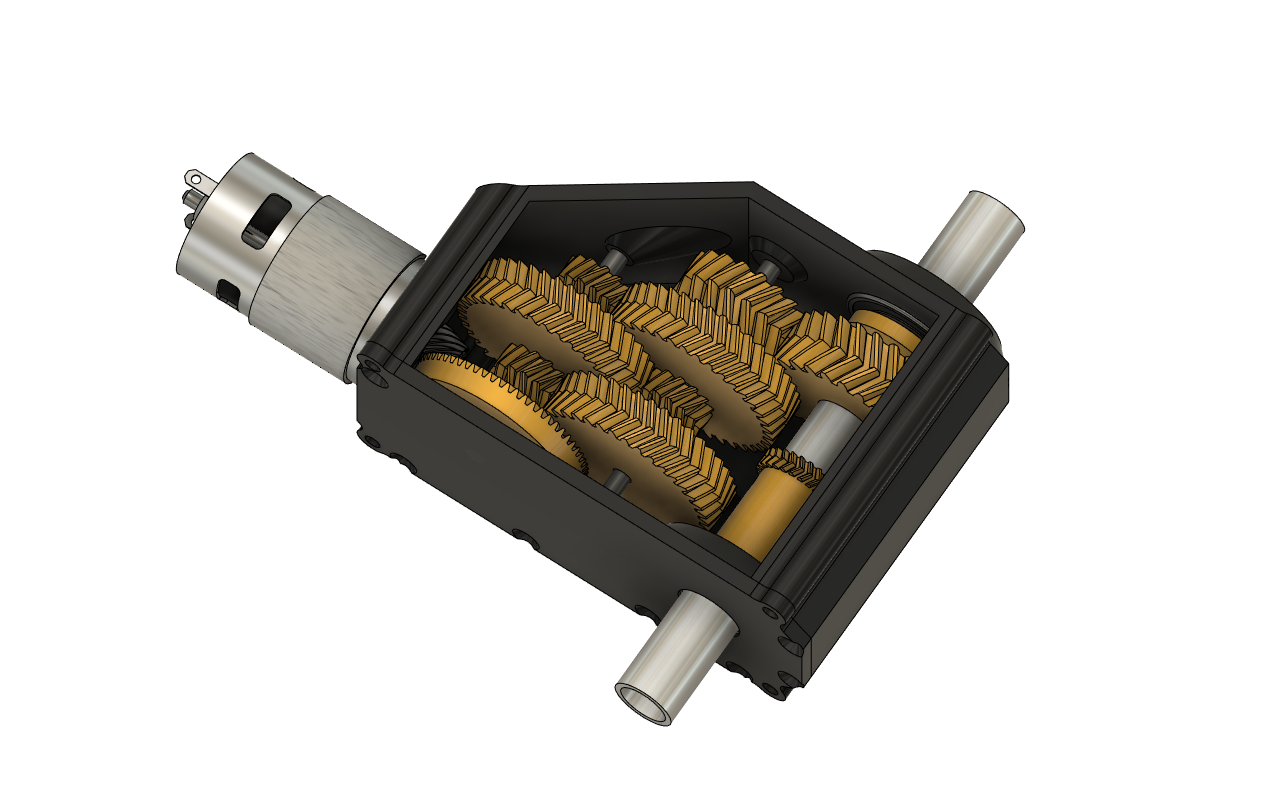
- Define clear project requirements
- Choose appropriate 3D modeling software
- Accurately model the servo motor
- Apply realistic load conditions
- Analyze and validate simulation results
(servo torque testing checklist, 3D modeling process, simulation validation)
What is servo torque testing?
+Servo torque testing is the process of measuring and analyzing the torque produced by a servo motor under various conditions to ensure optimal performance and reliability.
Why is 3D modeling important for servo torque testing?
+3D modeling allows for detailed visualization, simulation, and accurate prediction of servo motor torque, reducing the need for physical prototypes and saving time and costs.
What software is best for 3D servo torque testing?
+Popular software options include SolidWorks, ANSYS, and COMSOL Multiphysics, each offering robust tools for servo motor simulations and torque analysis.
In summary, utilizing a 3D model for servo torque testing enhances accuracy, efficiency, and cost-effectiveness. By following the steps outlined in this guide, engineers and technicians can ensure reliable results and optimized servo motor performance. (3D model for servo torque, servo motor optimization, torque testing guide)